Production Process of Hamachirimen
Our craftsmen put
their heart and soul into their work
Yoshimasa Orimono has integrated 38 processes in manufacturing,
starting from the procurement of raw material to shipment.
This is an introduction to the manufacturing process of Hamachirimen,
which is said to be the most exquisite white crepe.
Manufacturing Process of Weft Yarns

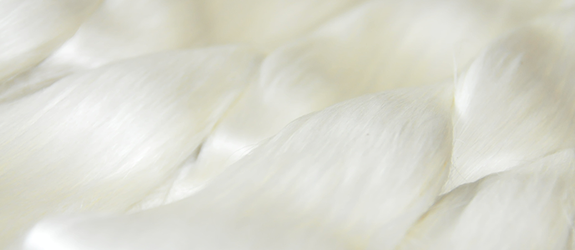
1.
Raw material
We use the highest quality raw material, "raw silk" in the world.
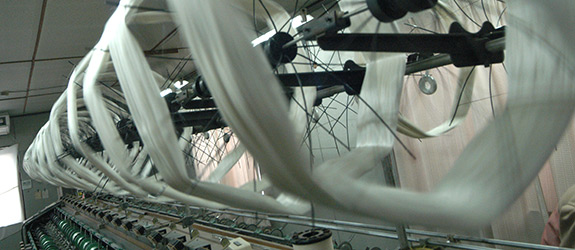
2.
Reeling
This is the process of winding skeins of raw silk onto a bobbin.

3.
Seven-ply doubling, three-ply doubling
Different types of Chirimen require different thicknesses and combinations of yarns.
Therefore, the right kind of yarn is required to be manufactured for each purpose.
During the doubling process, several threads of raw silk are pulled together and rolled onto a wooden frame.
The wooden frame can be either square or hexagonal. Hexagonal frames are more commonly used in recent times.
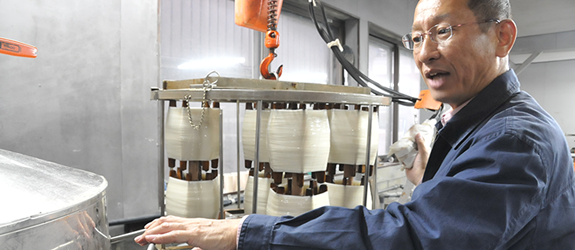
4.
Hot water soaking
When raw silk is soaked in hot water, a component called sericin that forms the outer layer of raw silk absorbs water and becomes puffy and soft.
As a result, the raw silk becomes soft, and the threads that are pulled together stick to each other.
This makes it possible to impart a high twist to the yarn during the processes that follow.
When sericin dries, it hardens and has a twist-setting effect.
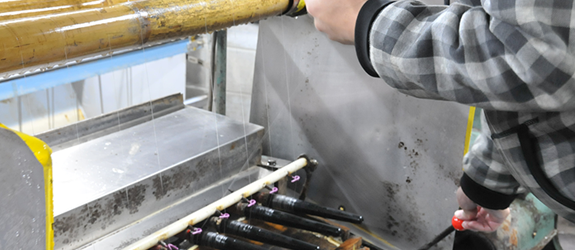
5.
Spindle winding
This is the process of winding the soaked raw silk on the wooden frames onto a spindle for the yarn twisting machine with water sprinkler, by dividing the yarns for right-twisting and left-twisting.
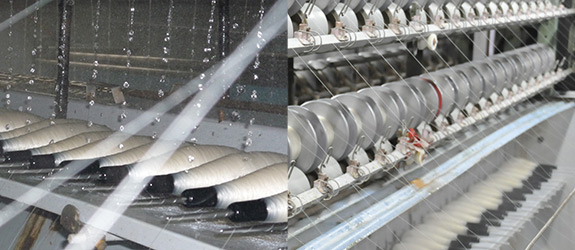
6.
Haccho yarn twisting machine
A twisting machine with a water sprinkler is used to add more twists to the raw silk wound on the spindle while sprinkling water to produce a predetermined number of twists.
* The next process after 7-ply doubling is final twisting.
11 To final twisting process →
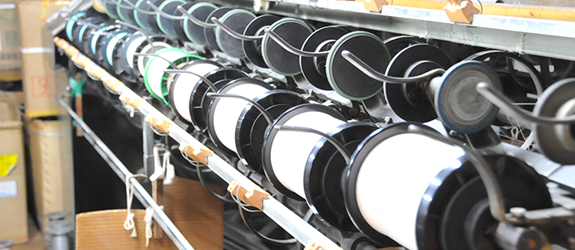
7.
Re-reeling after completion of first twisting of 3-ply yarn
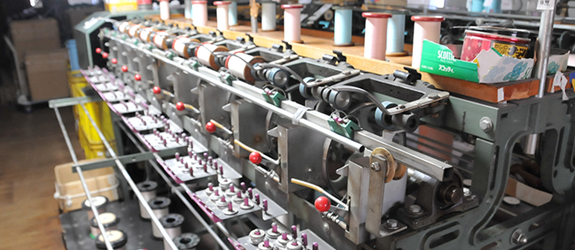
8.
Doubling for a corkscrew twist
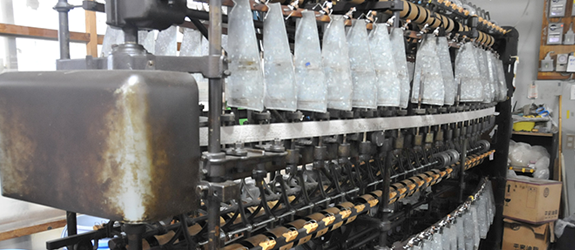
9.
Italian twisting (corkscrew twist)

10.
Corkscrew twist re-reeling
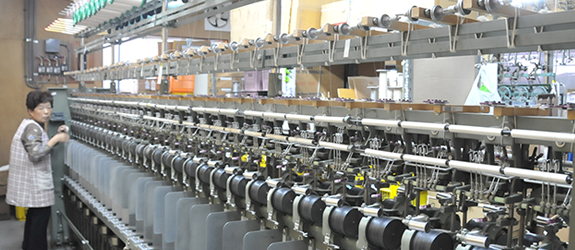
11.
Final twisting
This is the final process for the weft yarns used for Kawari Chirimen, where 7-ply Haccho twisted yarns, and corkscrew twisted yarns are combined and twisted further.
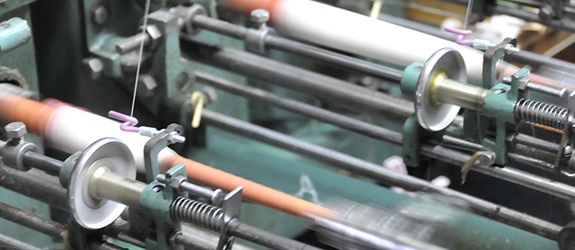
12.
Pirn winding
This is the process of winding the weft yarns made by final twisting onto the pirns for weaving on the loom.
* The subsequent processes are common for the weft and warp yarns.
To the manufacturing process that is common for weft and warp yarns -->
Manufacturing Process of Warp Yarns

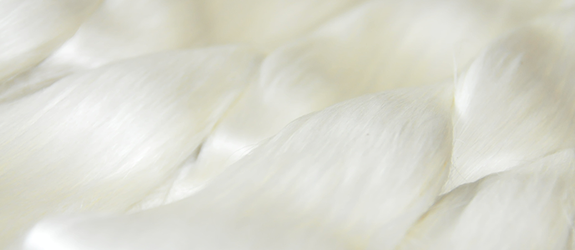
1.
Raw material
We use the highest quality raw material, "raw silk" in the world.
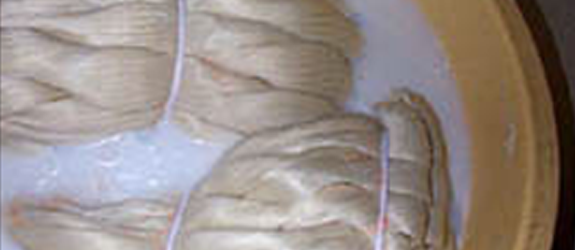
2.
Soaking
Several methods can be used for soaking. This is the process of adding slipperiness, softness and anti-static properties to the yarn by soaking it in oil or sprinkling oil on the yarn.
This makes it easier to handle the yarn in the processes that follow.
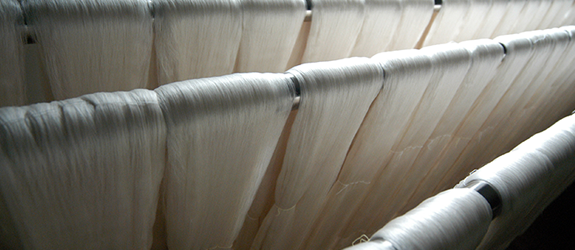
3.
Drying
Water is drained from the soaked raw silk and then placed on a pole to dry.
The raw silk is dried using methods that are closest to natural drying.
* Photograph of a skein.
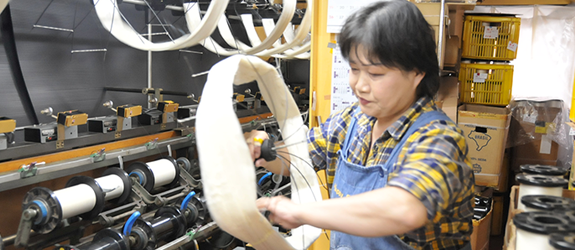
4.
Reeling
This is the process of winding skeins of raw silk onto a bobbin.
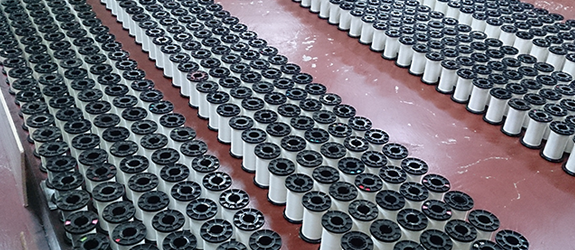
5.
Bobbin arrangement
Bobbin arrangement (Work of arranging the bobbins)
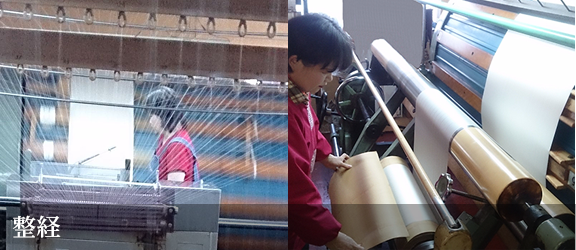
6.
Warping and winding
This is a pre-process to prepare warp yarns for the loom, where the number, length and width of the warp yarns are adjusted for each type of product.
Winding is the process in which yarn wound during warping is wound onto a beam for use in the loom.
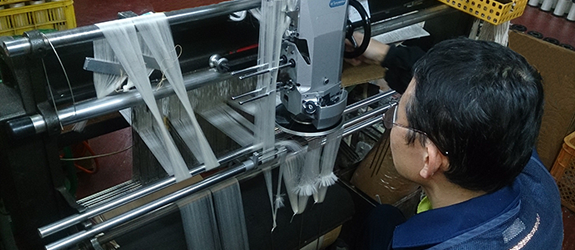
7.
Connecting warps
This is the process of connecting the finished warp yarns to the new warp yarns to continue weaving the Chirimen of the same dimensions as the one that was finished weaving.
This eliminates the processes of "threading" and "passing through the reed".
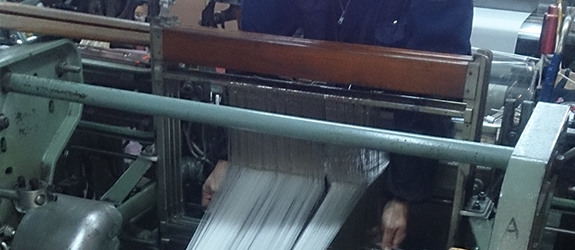
8.
Looming
This is the finishing process the warp yarns made in steps 7 and 8 on the loom.
* The subsequent processes are common for the weft and warp yarns.
To the manufacturing process that is common for weft and warp yarns -->
Manufacturing process common for weft and warp yarns

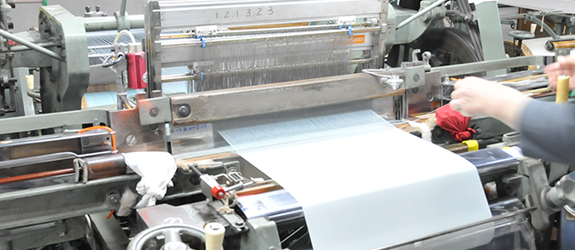
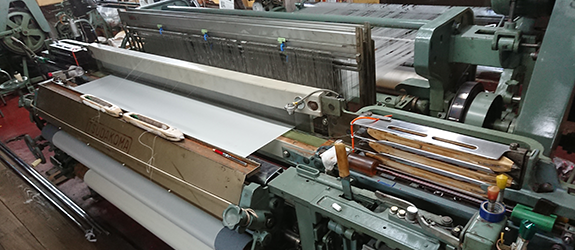
1.
Weaving
This is the process of weaving warp and weft yarns on a loom.
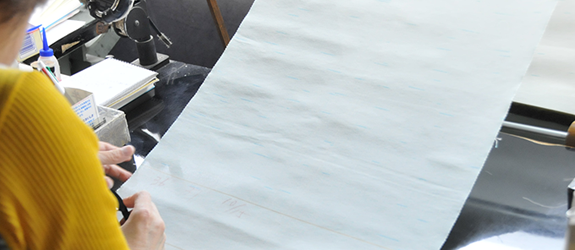
2.
Grey fabric inspection
This is the process of inspection of the woven grey fabric.
* Grey fabric refers to the fabric before scouring.
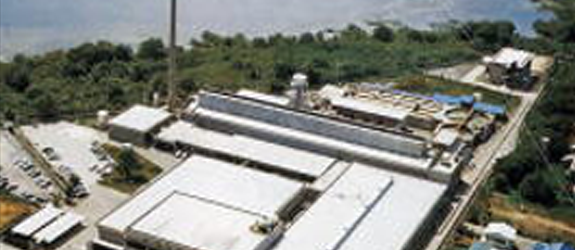
3.
Scouring and inspection by the Association
The grey fabric that has passed the inspection is sent to the common processing plant of the Hamachirimen Industrial Association for scouring and inspection by the Association.

4.
Product inspection
The finished products, which are scoured and inspected at the common processing plant of the Hamachirimen Industrial Association, undergo in-house inspection for each application following our standards.
Inspection methods include inspection by the reflection of natural light, examining the watermark under natural and fluorescent lights.
Products that pass the inspection at this stage are stamped with the Hamachirimen seal.
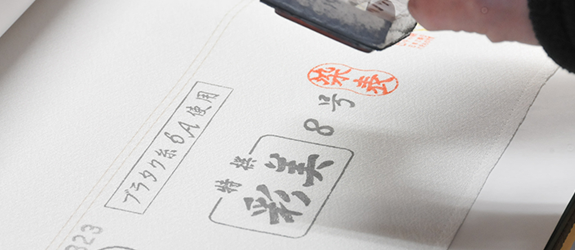
5.
Stamping of the mark
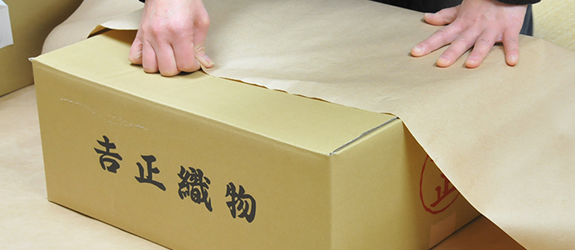
6.